Volkswagen's Lutz Meyer on getting from A to B...
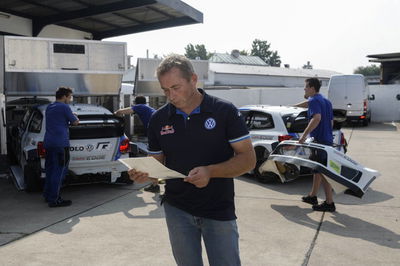
Seven shipping containers weighing 79 tonnes fully laden plus 18 tonnes of air freight: the three overseas rallies in Mexico, Argentina and Australia alone pose a huge organisational challenge as well as testing the team's sporting abilities.
Lutz Meyer is the logistics expert responsible for ensuring that everything needed for the three Polo R WRCs ends up in the right place.
In this interview - kindly provided by Volkswagen - he explains how the team overcomes this challenge and how the overseas rallies differ from events in Europe from his point of view....
Q:
When did logistical preparations for the 2013 World Rally Championship begin?
Lutz Meyer:
On 31 August 2012. That is the day we decided what the Volkswagen service area should look like at each rally. Before that, we had to think about a few questions, such as: How will the service tents be arranged? Where will we keep spare parts and tyres? Where is the engineers' office? Where do we want the kitchen and where will the team eat? Then the concrete planning began - and that was the hardest part, to be honest. The containers for overseas rallies in particular had to be designed and built exactly in line with our needs.
Q:
How do the logistics for European and overseas rallies differ?
Lutz Meyer:
We travel to rallies in Europe with seven trucks. One trailer holds all the recce equipment and another one contains the big office for the engineers and the team managers. Then there are two vehicle and parts trailers for the three Polo R WRCs, a lorry transporting the wheel rims, tyre racks and the cleaning unit, plus two equipment trucks. By contrast, we use containers to transport everything to overseas rallies and live out of the containers during the event. The seven shipping containers for our equipment, repair workshop, recce vehicles, service tents, kitchen and office weigh almost 48 tonnes unladen. When they are full, they weigh in at 79 tonnes. Then there are about 18 tonnes of air freight on top of all that.
Q:
Are the overseas and European rallies organised at the same time?
Lutz Meyer:
Yes, they have to be. Not all parts are always readily available. You can't just pack a shipping container full of parts if they are still needed in Europe. The rules stipulate that each team can only use a certain number of engines and gearboxes per season. These parts have to be flown to Mexico, Argentina and Australia just like the rally cars.
Q:
Is there some freight which doesn't go back to the team's base in Hanover at all during the season?
Lutz Meyer:
Yes, there is. It includes all the standard parts which are not limited in number by the rules, such as wheel rims, bolts and underbody protectors. We booked a round trip for this kind of cargo back at the end of last year. It went straight from the Rally Mexico in early March to Argentina by ship. Then it was shipped on to Australia starting in May. These containers will come home in November.
Q:
What additional organisational obstacles have to be overcome for sea freight?
Lutz Meyer:
There are quite a few. Australia has special quarantine rules, for example, so the shipping containers were checked by Australian inspectors before they even left Argentina. These inspectors used disinfectant bombs to kill all the germs on our parts. On top of this, right from the start the containers had to be designed so that they could be stacked anywhere on large freighters and at sea ports. The idea is to avoid having a container which can only ever be stacked right at the top because it cannot withstand the necessary stacking load. If other containers can't be stacked on top, it is more expensive.
Q:
How many days a year are you personally on the road because of the rallies?
Lutz Meyer:
On average, about one and a half weeks per rally.
Q:
And how much time do you spend taking care of formalities?
Lutz Meyer:
I must spend 60 to 70 per cent of my time at work filling in applications and other forms. There's an awful lot of paperwork. Luckily, I don't have to complete it all on my own - I work with the team manager who's responsible for the budget.
Q:
How many members of staff are involved in organising transport and setting up or dismantling the Volkswagen service area?
Lutz Meyer:
Our team consists of just six people. Then there are the team managers in addition to this, who take care of booking flights and so on. But basically, these six people are responsible for setting up and dismantling and for maintaining the equipment at the track. On top of all that, they look after tyre management during the rally. That means they take the wheel rims and used tyres to Michelin, collect the new fully assembled wheels, check the air pressure and make sure the right wheels are on hand for each car during servicing. That's really hard graft.
Q:
How much improvisation is needed before and during a rally?
Lutz Meyer:
As a rule, we've considered and planned everything beforehand, but there is always a chance that something might happen which we have to deal with spontaneously. For instance, each organiser allocates us a specific number of square metres in the service park. Despite detailed drawings and plans, we may find that there is a drain cover or a hydrant in the way of our structures. In that case, we talk to the organiser on the spot or ask the neighbouring teams whether they can spare half a metre for us. We always find a solution somehow - everyone involved in the service park helps one another.
Q:
On the subject of space, how did the team cope with the Rally Monte Carlo, where the whole shebang had to move from Valence to Monaco during the rally?
Lutz Meyer:
Monaco is hellish on that front. There is hardly any space there in the middle of the city right by the yacht harbour. You have to haggle over every centimetre and no one has any time. We were really glad we only entered two cars there this year as it quite simply meant we needed a bit less space. We were also able to assemble our new set-up in Valence while we reused last year's structures in Monaco. That meant we could make the move pretty quickly.
Q:
As you just mentioned, Volkswagen Motorsport has been entering three Polo R WRCs since the Rally Portugal. What has changed for the logistics as a result?
Lutz Meyer:
It takes longer to set up and dismantle everything because there's an extra tent and there are simply more parts all over the place. But we allowed for that right from the start and included all the additional parts in the original shipments. That meant we had all the parts for three cars with us in Mexico even though we only entered two cars in the competition. After all, we had to contest the Rally Argentina with three Polo R WRCs two months later with the same set of overseas equipment.
Feature kindly supplied by Volkswagen Motorsport